前々回(鋳造)と前回(鍛造)の記事では、それぞれの製造方法やメリット、デメリットについてそれぞれ解説してきました。私が自動車エンジニアとして関わった部品はクルマの部品点数の中ではごく一部ではありますが、量産車においてコストと性能、品質はかなりシビアです。その中で実際に採用されている技術は、厳しい基準をくぐり抜けてきた選びぬかれた技術です。今回の記事では、そのような実際に採用されている製造技術(鋳造 or 鍛造)について、部品ごとに解説していきます。
アルミホイール
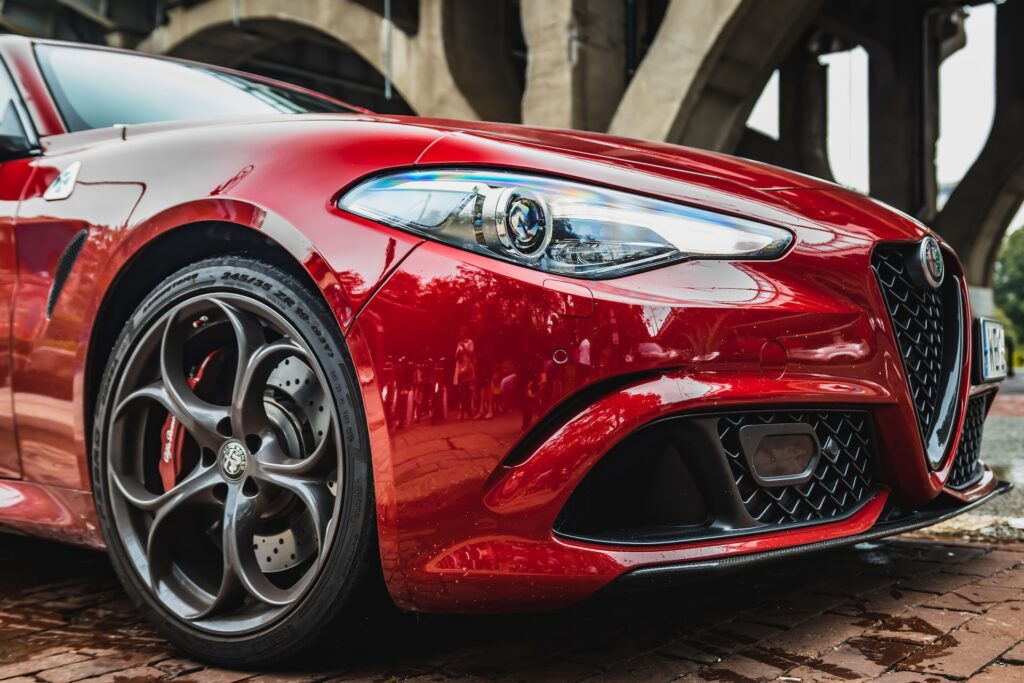
量産車のホイールには鉄製と鋳造アルミホイール製、一部に鍛造アルミホイール製があります。昔は鉄ホイールが主流でしたが、現在では鋳造アルミホイールが乗用車の多くを占めています。
鋳造アルミホイールの利点はデザインの自由度が高く、切削加工などによる意匠性が高いことです(それだけとも言えます)。一般的には鉄ホイールの方が軽く作ることができます。その理由は、ホイールは剛性設計ではなく強度設計で作られるからです。実のところ、ホイールは入力点の端部(タイヤ)に近いため、剛性はあまり求められません。釣り竿の先が細く、根元は太いのと同じ原理です。一方、路面からの入力や衝突安全性の要件から、ある程度高い強度が求められます。アルミは単純な引張強度で鉄には及ばないため、鉄ホイールの方が軽く作ることができるのです。また、鉄は靭性が高いため、アルミホイールであれば歪むような衝撃に対しても、ある程度変形していなすことができます。商用車やオフロードモデルで鉄ホイールが採用されるのはこのためです。
さらに軽さを求めると鍛造アルミホイールになるのも同じ理由です。鍛造にすることでアルミの強度や靭性を補うことができるため、高価ですが理にかなっている鍛造部品だと言えます。
サスペンションアーム
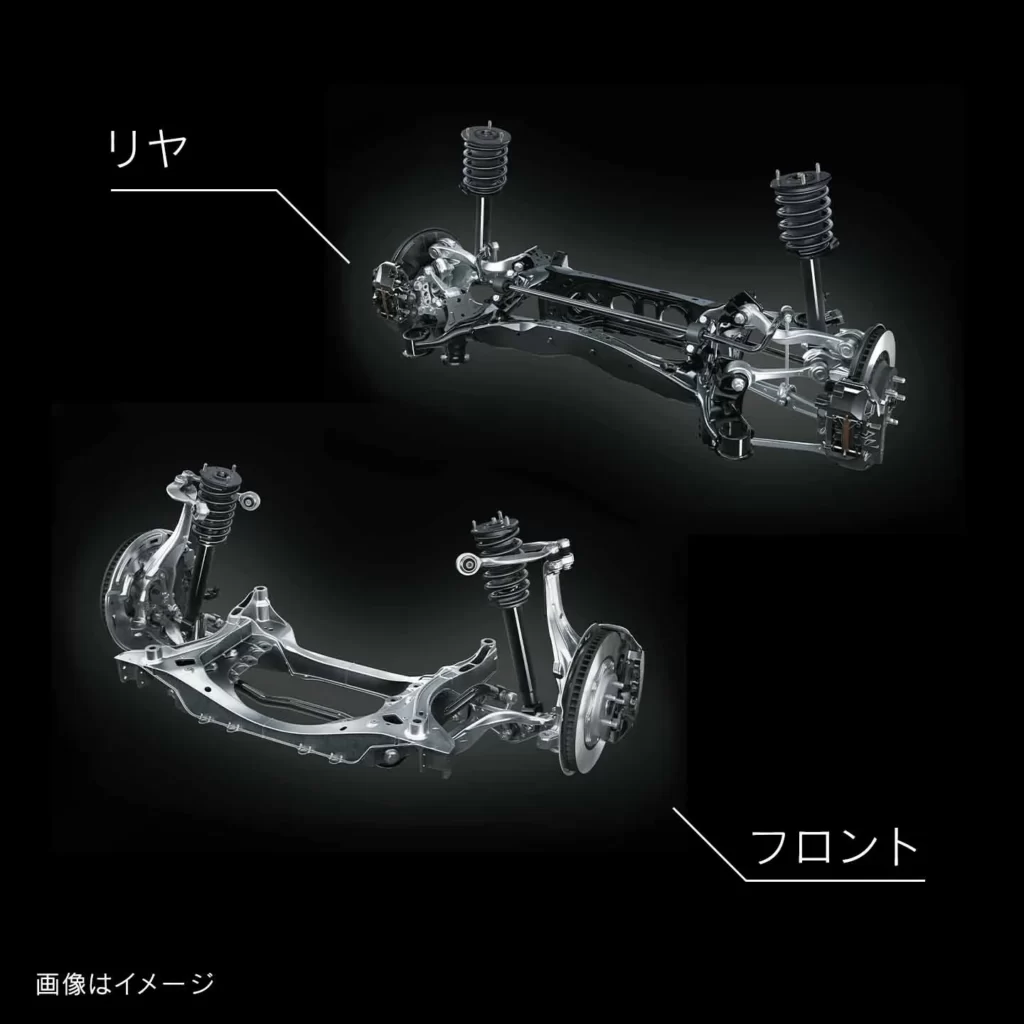
コンパクトカーなどの主流は板金プレス品(鉄)のサスアームが多く、軽量化のためにアルミ鋳造品やアルミ鍛造品が使われることもあります。シビックタイプR(FL5)の場合、フロントサスのロアアームやダンパーフォーク(デュアルアクシスストラットにおけるナックルとストラットを繋ぐ部品)はアルミ鍛造品、ナックルは形状が複雑なためアルミ鋳造品が採用されています。ストラット式サスペンションのアームには曲げ入力も加わるので、断面の大きさで剛性を確保する形状になっています。
一方、FRのリアサスに使われるマルチリンクのサスアームには、シンプルな丸鋼管(鉄の中空断面)が多く使われます。マルチリンクのサスアームに働く曲げ入力は小さく、アームの長手方向に引っ張ったり縮めたりする入力が大きいため、断面を大きくせず単純な丸中空断面にしています。単純な引張や圧縮の入力であれば、あえてアルミにするよりも鋼管の方がコストと強度で有利です。
シリンダーブロック
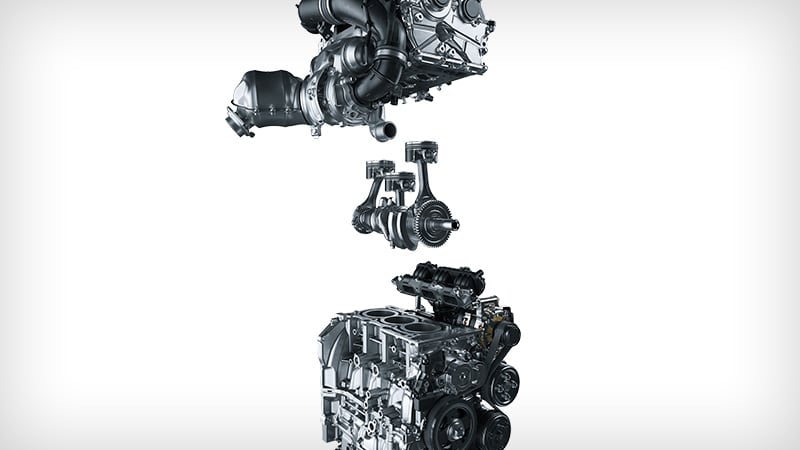
シリンダーブロックはアルミ鋳造品が多く使われていますが、昔は鋳鉄製が一般的でした。大型ディーゼルエンジンは今でも鋳鉄製のシリンダーブロックが使われています。シリンダーブロックは深さがある中空構造なので鍛造では作れず、アルミか鉄の鋳造です。
コストを掛けることができる高性能エンジンでは、ダイキャストではなく砂型鋳造で作られることがあります。砂型鋳造の最大のメリットは中子(なかご)を使ってエンジン内部の複雑な冷却水路や、強度が高い内部構造を作れることです。クローズドデッキと呼ばれるシリンダーブロックは砂型鋳造で作られ、ダイキャストで作るオープンデッキのシリンダーブロックのようにシリンダー付近の冷却水路が『オープン』になっていないので、高いシリンダー圧力に負けないシール性や強度を確保できます。
GRヤリス/GRカローラのG16E型エンジンはクローズドデッキを採用する一方、シビックタイプRのK20C型エンジンはオープンデッキ、というように高出力エンジン=クローズドデッキと言うわけではありません。
コンロッド
コンロッドは鍛造の鉄製です。汎用小型エンジンではアルミ製もあるようですが、自動車用エンジンでは高い強度が求められるため、鍛造鋼一択です。形状としても丸棒の鍛造鋼をプレスして作るのに適していると言えます。
クランクシャフト
かつては鋳造品が多かったものの、高強度と軽さのために鍛造品が主流になりました。一本の鍛造鋼の丸棒からクランクピンやカウンターウェイトを成形します。さらにV8などクランク位相差があるエンジンの場合、1000℃以上の高温を保ったままツイストされます(ねじり工程)。高温状態で剛性をある程度保ち、固体のまま成形したりねじったりできるのが鍛造鋼の特徴でもあります。
ピストン
最近のエンジンのピストンはアルミ鋳造品とアルミ鍛造品が使い分けられています。鍛造品の方がコストが掛かり、高価になりがちですが、軽量化のメリットを最大限に発揮できる二輪車の高性能スポーツモデルなどに採用されています。鋳造ピストンには複雑な形状にできるというメリットがあり、近年の鋳造ピストンは鍛造ピストンに迫る強度と軽さを実現しています。
ちなみにマツダの2.2L直4ディーゼルはアルミ製でしたが、最新の3.3L直6ディーゼルはスチールピストンになっています。
ブレーキキャリパー
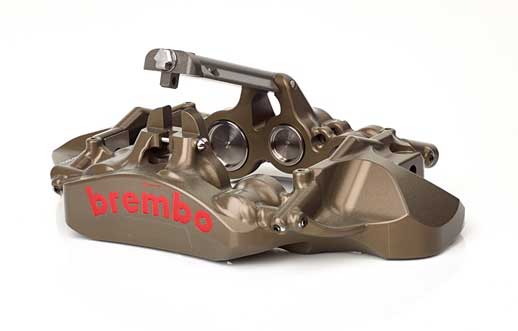
ブレーキキャリパーにはアルミの鋳造品が多いものの、一部レース用などで鍛造品が使われます。ブレーキタッチ向上のために高い剛性が求められ、ばね下の重量物にあたるので軽さも求められます。通常は2ブロック構成でボルトで挟み込む構造をしていますが、これを軽量高剛性化するためにアルミの塊から機械加工で削りだしたモノブロックキャリパーがあります。レース用では剛性よりもギリギリの強度で軽く作るため鍛造アルミブロックをさらに機械加工したものもありますが、下手に加工すると重要な鍛流線を切ってしまうことになるので高い技術が必要です。。
また、キャリパーだけを高剛性化したとしても、ブレーキホースや取り付け剛性などのトータルでブレーキ性能が決まるので、高価なモノブロックキャリパーを付けても劇的な高性能化は難しいといえます。しかし、アルミ削り出しのモノブロックキャリパーはかなり目を引くので、本物感を持たせるためのドレスアップパーツとして優秀です。
まとめ
今回は自動車の特徴的な部品ごとにその製造方法を解説しました。また気になった部品や、EV化による新たな部品と材料技術があれば取り上げていきたいと思います。
コメント