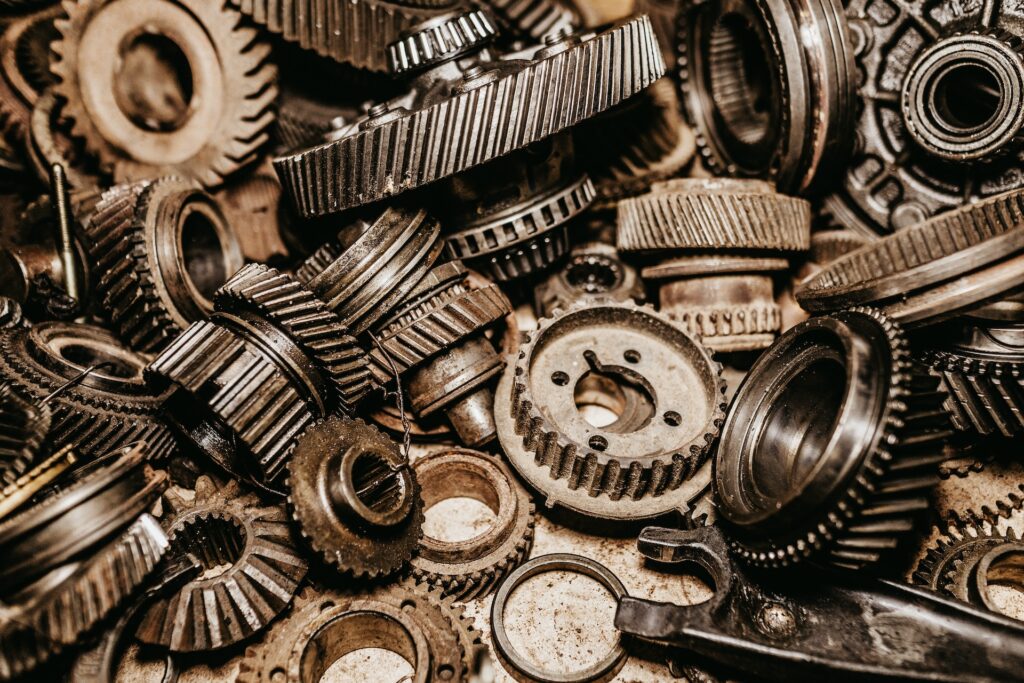
クルマには様々な部品があり、部品によってその製造方法は様々です。なかでもエンジンなどの重要部品を作る鍛造(たんぞう)と鋳造(ちゅうぞう)の技術は、クルマづくりには欠かせません。クルマの電動化が進むことでエンジンが無くなり、鍛造や鋳造で作ってきたエンジンの主要部品がなくなる一方で、電動化されたクルマにもこれらの製造技術は使われていきます。特にアルミの鋳造品は電気モーターのケースやeアクスル、インバーターケース、駆動モジュールなどに多く使われています。
本記事では、鍛造と鋳造にどんな技術が詰め込まれているのか、クルマの電動化とも関連付けながら現役自動車メーカーエンジニアが紹介していきたいと思います。
![]() | 【新品】モーターファン・イラストレーテッド 図解・自動車のテクノロジー Volume199 特集鍛造と鋳造 価格:1,760円 |

鍛造(たんぞう)と鋳造(ちゅうぞう)の違い
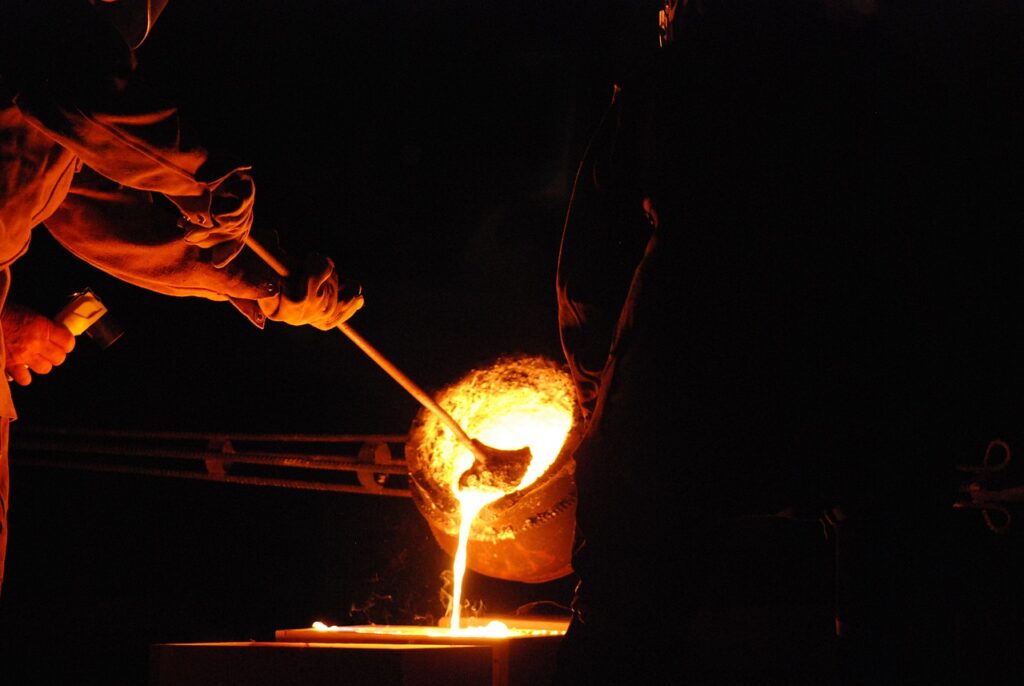
鍛造(たんぞう)と鋳造(ちゅうぞう)の違いを簡単に説明すると、鍛造は個体から形を作り、鋳造は液体から形を作ります。鍛造はハンマーやプレス機を使って素材となる金属の塊を変形させます。この変形は金属の靭性(じんせい、割れずに伸びる性質)を利用しており、強度を高めつつ軽く作ることができます。一方の鋳造はドロドロに溶かした金属を型に流し込んで形を作ります。素材自体には鍛造ほどの強度はありませんが、形状の設計次第で剛性や強度を効果的に高めることができ、中子(なかご)を使うことで中空構造も作れます。部品によっては鍛造品以上に軽量化できる場合もあり、鍛造の下位互換ではありません。
鍛造(たんぞう)のメリット
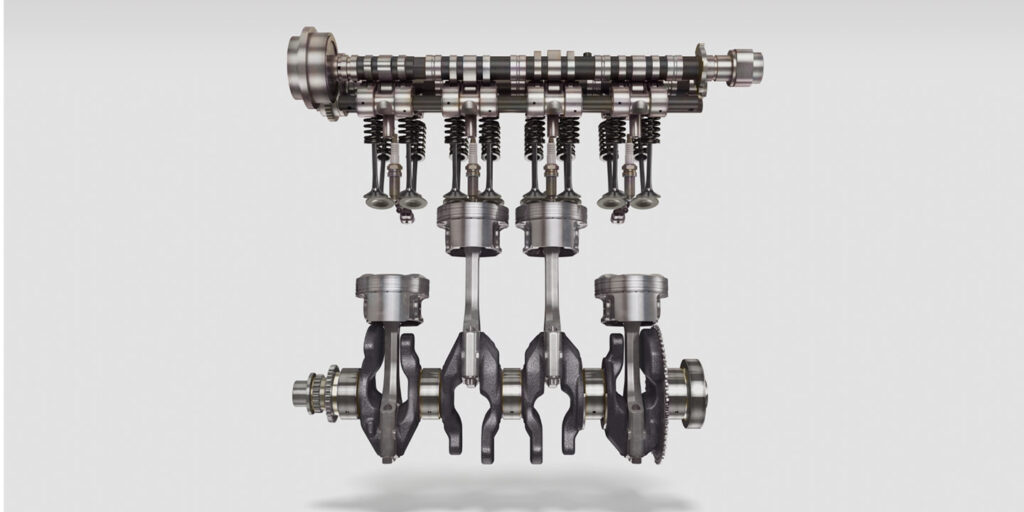
巨大なプレス機でアルミや鉄などの金属を圧縮成形することで素材が持つ強度を高め、気泡などの欠陥を無くして高い品質の製品を作ることができます。鍛造品は鋳造品に比べ、強度や靭性(じんせい)が高いという特徴があります。この特徴を生かして鋳造品よりも軽くできるのが最大のメリットです。
鍛造で剛性は高くならない
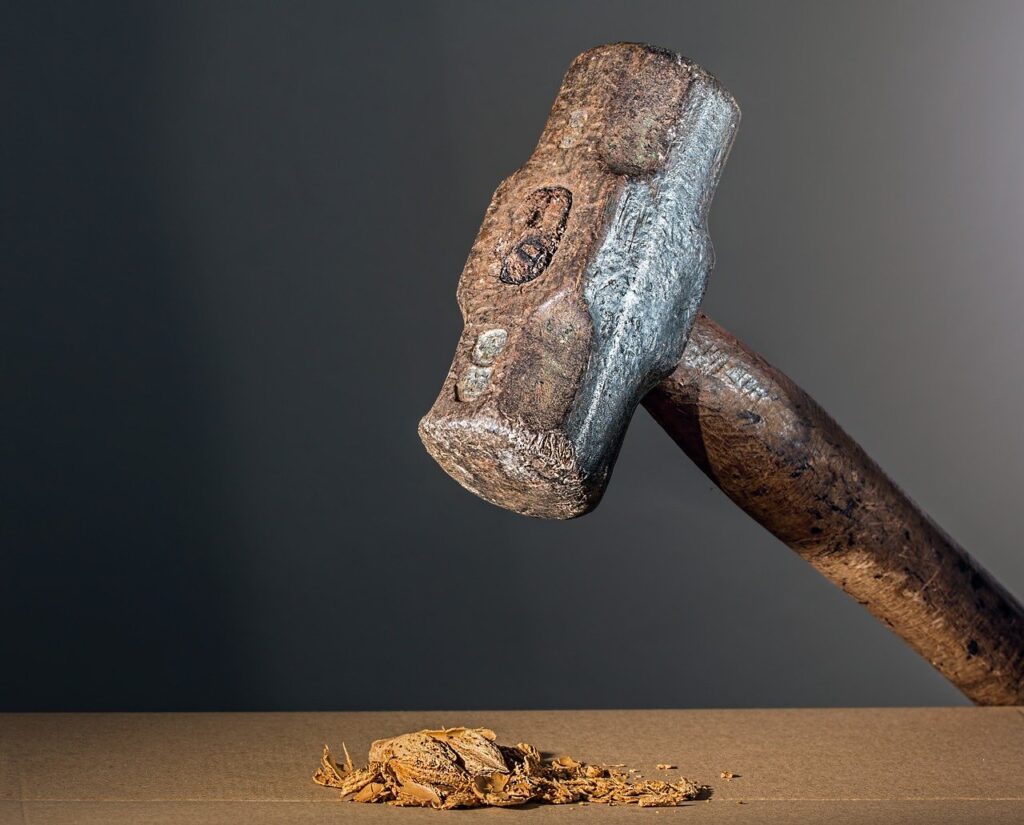
鍛造で得られる強さは強度と靭性であり、剛性は高くなりません。強度と剛性の違いについては過去の記事でも解説しています。剛性は金属元素の分子間に働く力で決まります。そのため、鍛造の過程で剛性は変化せず、剛性は素材そのものの組成(各金属元素の割合)で決まります。
アルミの場合、鍛造材と鋳造材で組成は異なるものの、ヤング率(素材の剛性)はどちらも約70GPaで同等です。そのため、製品形状が同じであれば鍛造だろうと鋳造だろうと剛性は変わりません。
鉄の場合、鍛造鋼のヤング率が約205GPaであるのに対して、鋳鉄は約175GPaと小さくなります。そのため、製品形状が同じであれば鋳造よりも鍛造のほうが17%程度剛性が高くなります。これは後述する鍛流線などの結晶構造による違いではなく、組成の違いによって生じます。
製品形状を複雑にできるので、鋳造の方が剛性を高くしやすい傾向にあります。特にアルミの場合、鋳造品の方が剛性を高める形状(リブなど)を作りやすいので、剛性が求められる製品には鋳造品が適していることが多いです。アルミ製のサスタワーが鋳造品であることも剛性を高めるためだと考えられます。
鍛造で得られる靭性とは
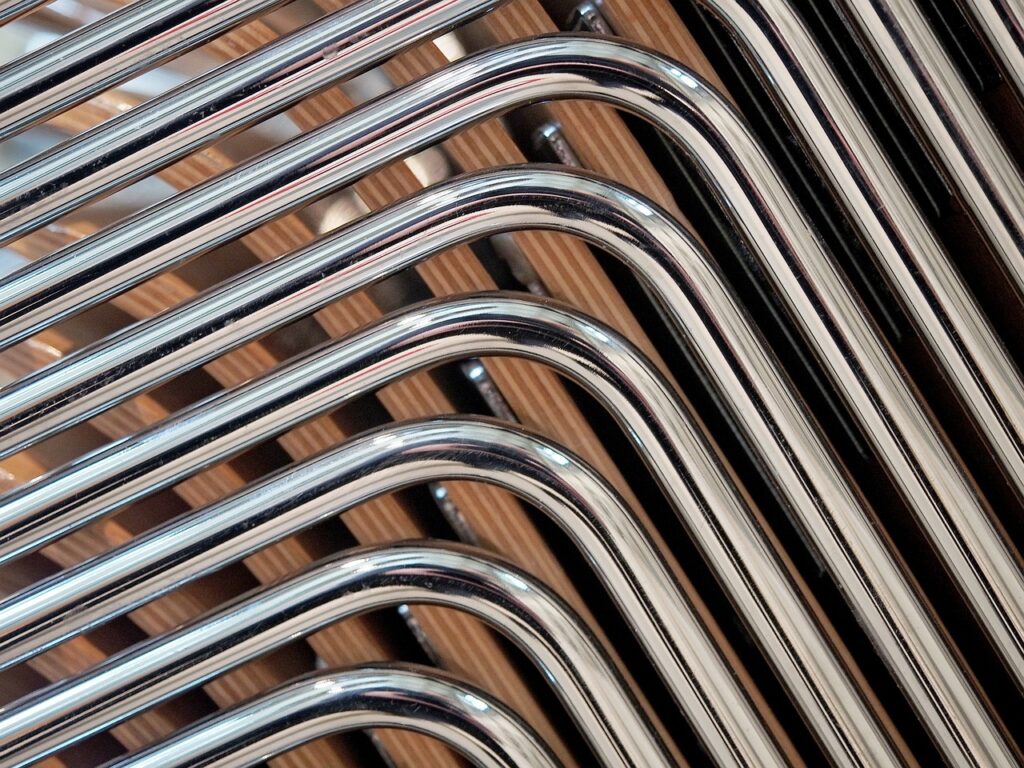
鍛造で得られる靭性(じんせい)とは、靭(しな)やかであること、粘り強いこと、と表現されます。その特性とは、力を加えたときに壊れる前に材料が伸びることを指します。どの材料でも多少は伸びますが、『靭性がある材料』というと、その伸びが比較的大きい材料を指します。
伸びると何が良いのかと言うと、衝撃に強いということです。同じ強度を持った材料でも、壊れるまでに材料が伸びることで衝撃(ここではエネルギーの意味)を吸収してくれます。物理学的に『エネルギー = 力 × 距離』なので、同じ強度(力)でも材料自体が伸びることで距離を稼ぎ、衝撃を吸収してくれるというわけです。強い衝撃でアルミホイールが歪みやすく、鉄ホイールが歪みにくいのは鉄自体が靭性を持っているからです。
鍛造品が靭性を得られる理由は、製品内部の金属結晶構造にあります。鍛造で作られた製品の内部には鍛流線(たんりゅうせん)と呼ばれる模様が入っています。
鍛流線(たんりゅうせん)とは
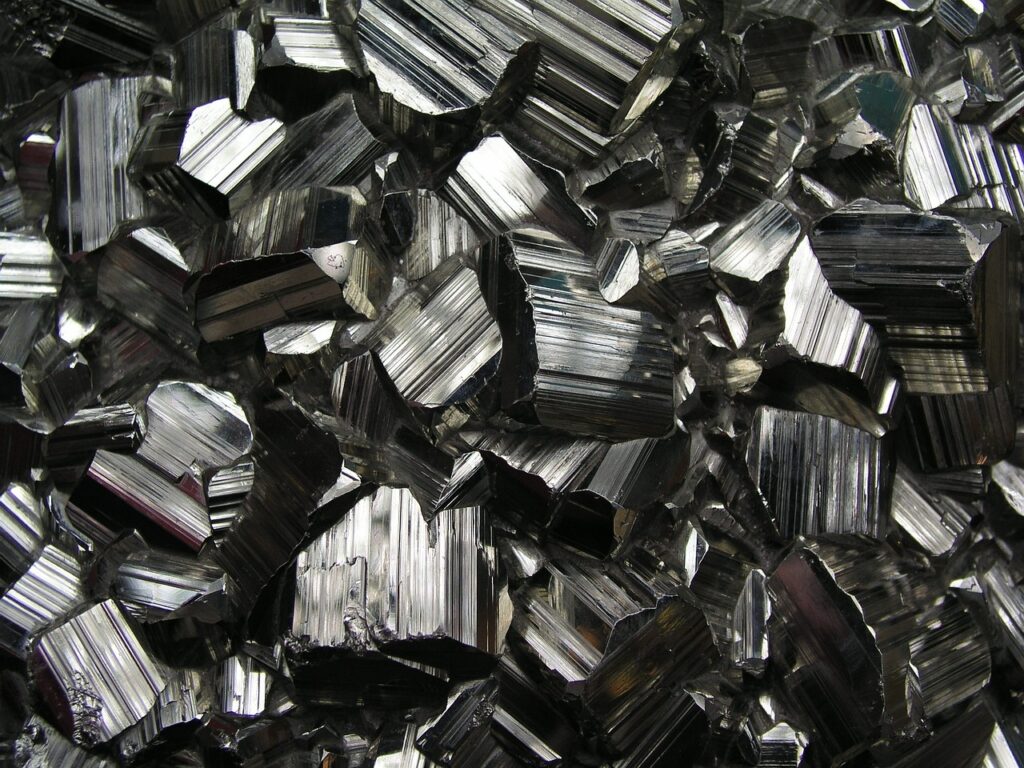
鍛造鋼(たんぞうこう)の丸棒内には木の年輪のような模様が入っています。これは鍛流線(たんりゅうせん、ファイバーフロー)と呼ばれており、金属の結晶が潰れたり引き伸ばされたもので、断面を見ると地図の等高線のように見えます。鍛流線の方向に力が加わった場合、強度や靭性が高くなります(引張強さは変わらない)。鍛流線の方向が入力方向と直行していたり、切削加工などで分断されていると、鍛造のメリットが半減してしまいます。
一方、鋳造品の断面はカクカクした結晶構造が見られます。これは液体の金属が冷えて固まるときに小さい結晶が散発的に発生し、それぞれの結晶が成長することで形成されます。
熱間鍛造とは
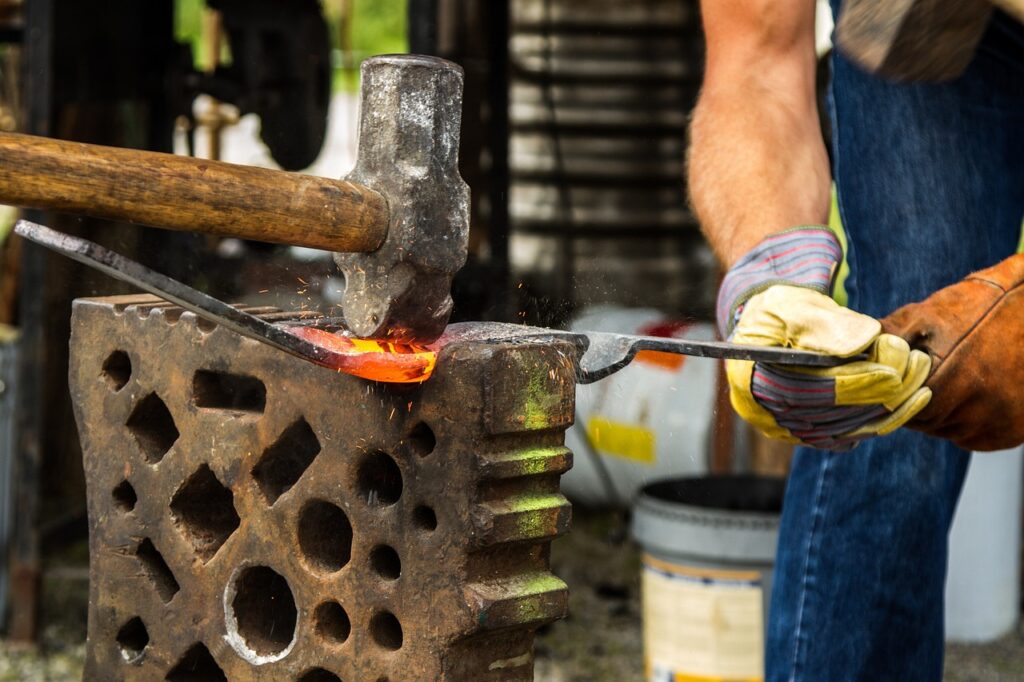
熱間鍛造の場合、鍛造用の素材を加熱してからハンマーやプレス機で力を加えて成形します。金属によって異なるものの、素材となる金属の融点の約80%程度の温度まで加熱されます。加熱によって鉄系材料はオーステナイトという組織になり、鉄元素の間に炭素など他の元素が入り込んだ構造になります。この状態で成形した後で適切な熱処理(焼入れ)を行うことで硬い組織(マルテンサイト)を持つ製品になります。
冷間鍛造とは
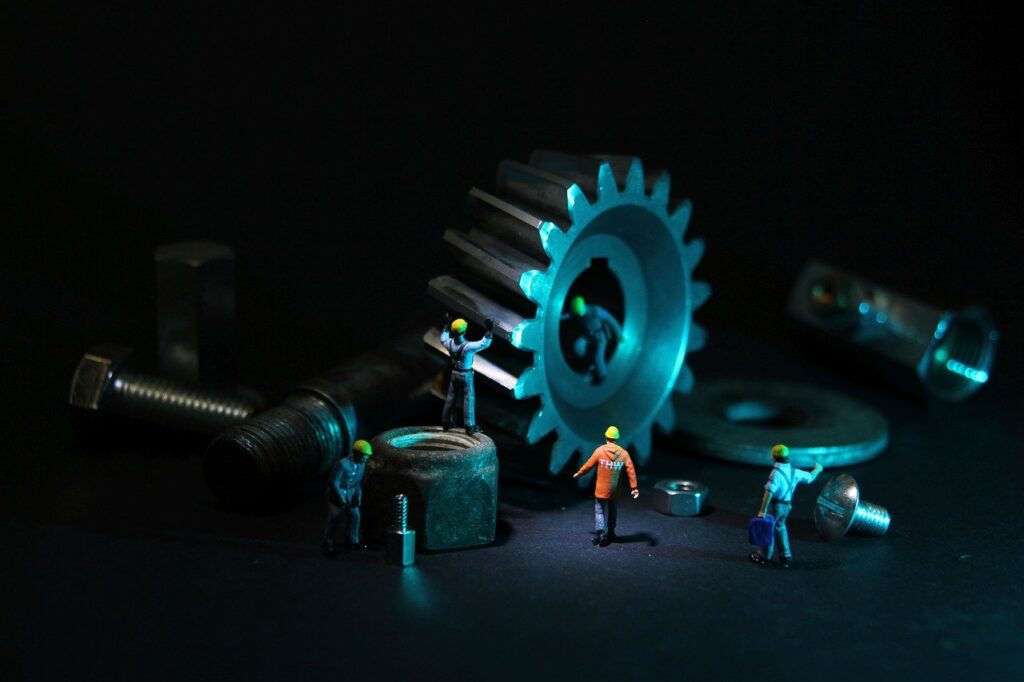
冷間鍛造の場合、素材を加熱せず常温で成形します。熱間鍛造と比べた時のメリットは、製品の精度の高さです(形状精度、寸法精度)。また、加熱冷却する時間が不要なので生産性が高く、エネルギーコストも抑えられます。また、精度が高いため、ねじ山を後から加工する必要がありません。加工コストが抑えられるだけではなく、加工によって鍛流線を切らないので鍛造のメリットを活かすことができます。
冷間鍛造で作られた製品が高精度である理由は、加工後に体積の収縮や膨張が少ないことです。鉄系材料の熱間鍛造ではオーステナイトという組織になるまで加熱しますが、オーステナイト組織になるときには加熱しているのに材料が収縮します。逆に冷却するときには膨張することになり、一般的な熱膨張と合わせてこれらの特性を見込んだ加工が必要になります。また、加熱によって表面に酸化物が生成されることもないので、表面がきれいで滑らかに仕上がります。
近年の自動車業界では電動パワートレインの小型軽量化が求められており、高精度・高強度の特徴を生かして高出力モーターのトルクを受け止めるシャフトなどに冷間鍛造が使われる例があります。
今回のまとめ
今回は鍛造と鋳造の違いと、鍛造のメリットについてまとめました。鍛造は液体の金属ではなく、固体の金属に力を加えて加工する方法です。鍛流線と呼ばれる結晶構造をコントロールすることが鍛造のキモですが、それによって得られるのは強度と靭性であり、剛性は変わりません。
私は仕事柄、板金プレス部品を扱うことが多いですが、薄い鉄板のプレス成形と比べると鍛造の設備はかなり大掛かりで、職人技術の要素が大きいと感じます。どちらも昨今はCAEによる製品設計や成形シミュレーション、設備設計が欠かせない技術になっています。鍛造と聞くと刀鍛冶のような職人がハンマーで鉄を叩く姿を思い浮かべがちですが、現代の鍛冶職人はキーボードも叩かなくてはいけません。
次回の記事では鋳造のメリットと種類について解説します。
![]() | 【新品】モーターファン・イラストレーテッド 図解・自動車のテクノロジー Volume199 特集鍛造と鋳造 価格:1,760円 |

コメント